Achieving Net Zero in the Steel Sector
The challenge for the steel sector – and the world – is to reduce the emissions from steel-making to net zero by 2050 and a better benchmark mechanism could form a piece of the puzzle to deliver net zero steel, writes Matthew-Wenban Smith.
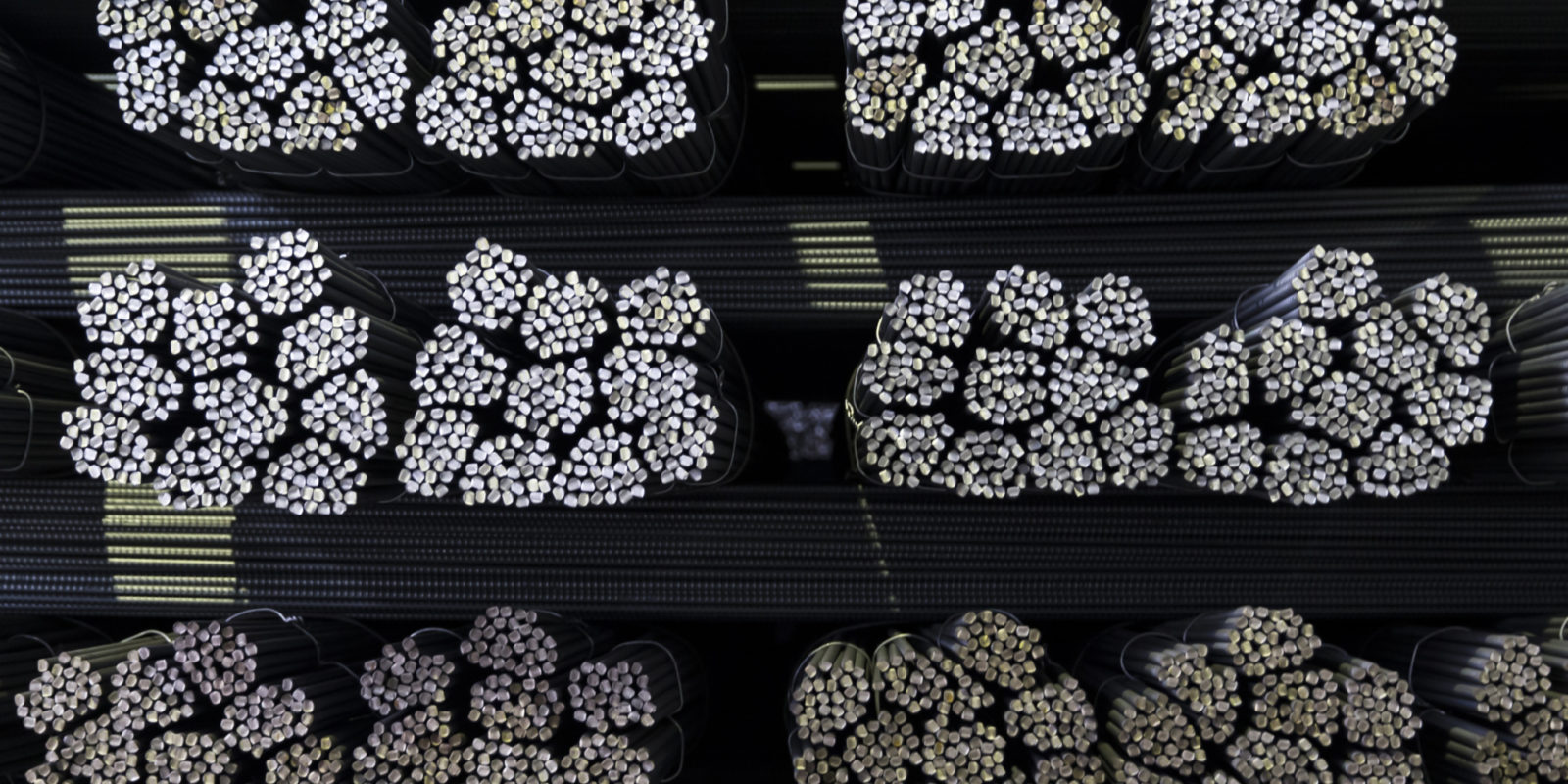
Bundles of finished steel rebars, manufactured from scrapped metals using electric furnaces at a factory, sit in a storage hangar ahead of shipping. Image: Tomohiro Ohsumi/Getty Images.
The steel challenge
The world uses a lot of steel – 1.9 billion tonnes of it in 2020.1 Bridges, buildings, railways, cars, rockets and wind turbines – they’re all made with steel.
To make that steel, 3.7 gigatonnes (Gt) of carbon dioxide was emitted to the atmosphere. 2.6 Gt in direct emissions and a further 1.1 Gt of indirect emissions2 which is about 9 per cent of the world’s total greenhouse gas emissions not related to land use.3 The challenge for the steel sector – and the world – is to reduce the emissions from steel-making from 3.7 Gt to net zero by 2050.
One way to manage the challenge would be to use less steel. In the US, there is around 10 tonnes of steel in use for every man, woman and child in the country. In India and Nigeria, the equivalent figures are 0.4 tonnes and 0.1 tonnes respectively.4
Population growth and rising living standards are expected to drive increasing demand particularly in Asia and Africa.
Set against that, the world can use steel more efficiently – using less steel to do more, or replacing steel with other materials, such as wood for construction.
Long-term projections for steel demand are inherently uncertain being sensitive to the assumptions made about how steel will be used in the future. The International Energy Agency’s Stated Policies Scenario, for example, projects global steel demand in 2050 as approximately 2.5 billion tonnes5 – a 30 per cent increase compared to today. In contrast, its Sustainable Development scenario, which builds in growing efficiencies of use, projects demand of just over 2.0 billion tonnes.6
The Net-Zero Steel Initiative has recently proposed a 'high circularity' scenario in which policies, such as car sharing and ‘virtual work’, are maximized and demand in 2050 is reduced to 1.8 billion tonnes.7
The bottom line is, even under the most resource-efficient scenarios, the world is expected to be using a lot of steel in 2050, and the fundamental question is, however much steel is produced, how do we reduce the emissions associated with its production to net zero?
Iron ore, scrap and greenhouse gas emissions
The ‘emissions intensity’ of crude steel – the volume of carbon dioxide equivalent emitted per tonne of crude steel produced – varies widely.
Figure 1 shows the emissions intensity of crude steel production at 290 representative sites in Europe, America, China, India and the far east in 2019, as modelled by CRU. It includes upstream and direct emissions as well as those from the external generation of energy.
The emissions intensity is plotted against the proportion of scrap used as an input material at each site. Steel-makers on the left of the graph are making steel with a high proportion of iron ore while those on the right are using a high proportion of scrap.
The graph tells us two things. One may be surprising but the other is not. The first is that the more scrap that is used as input, the lower the greenhouse gas emissions per tonne of steel is produced.
That is not surprising. It takes a lot of energy to separate the oxygen from the iron atoms in iron ore and much less energy to make steel from scrap when this has already been done. The average emissions intensity of steel-making from scrap is less than 25 per cent of that for making steel from iron ore.
The surprise is that there is such a wide variation in the proportion of scrap used. There are two main ways to make steel: the blast furnace-basic oxygen furnace route using iron ore as an input material and then the electric arc furnace route using scrap as an input material.
However, variations of these methods exist. In practice, the proportion of scrap used in a blast furnace can vary widely and up to 100 per cent of the input material for an electric arc furnace may be iron produced from iron ore.
Figure 1: Representative data for greenhouse gas emissions intensity of steelmaking sites
Source: Underlying data from the CRU Steel Cost Model and Emissions Analysis Tool (2021)
Today, most of the energy used to make steel – whether it’s made from iron ore or scrap, and in a blast furnace, basic oxygen furnace or an electric arc furnace – comes from fossil fuels, in particular, coal or natural gas.
The electricity used in an electric arc furnace could be generated from renewable sources rather than fossil fuels, which is a challenge of scale, not of technology.
In contrast, replacing coal or natural gas as the fuel in a blast furnace is a significant technical challenge. It can be done by using biofuels or hydrogen or by direct electrolysis of the iron ore.
Carbon capture to prevent emissions entering the atmosphere could also help reduce emissions from steelmaking. But none of these solutions is cheap, quick or easy to scale.
Scrap: A limited resource
It might seem, then, that there’s a simple way to reduce the greenhouse gas emissions from steel-making – just use more scrap and less iron ore and make steel in electric arc furnaces from renewable sources.
The problem is that the supply of scrap is limited. Steel is, in principle, infinitely recyclable but you can’t recycle it unless you have first made it and used it. The average lifetime of steel in a building is 30 to 40 years and can be much longer. Its average life in a car is around 12 years. And it’s estimated that 84 per cent of globally available steel scrap is already recycled. The quantity of scrap available for recycling cannot be quickly increased.
Scrap currently accounts for around 30 per cent of the iron bearing input material for steel making, with the remaining 70 per cent from iron ore. Under the International Energy Agency’s Sustainable Development scenario, the proportion of scrap rises to 45 per cent in 2050 with the remaining 55 per cent being made from iron ore. Even the Net-Zero Steel Initiative’s ‘high circularity’ scenario has iron ore accounting for around 28 per cent of production in 2050 assuming the ‘maximum employment’ of policies for material recirculation, production and material use efficiency worldwide.
If such maximum employment is not achieved then more iron ore will be needed. In the very long term it is inevitable that most steel will be made from scrap but the supply of scrap can’t be increased at the required scale and on the timeline needed to address the climate crisis.
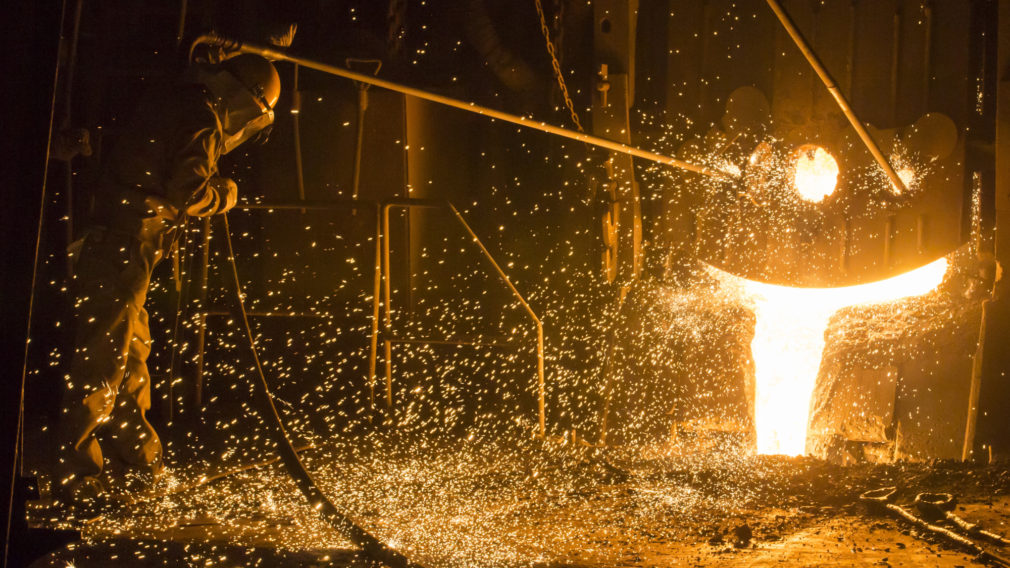
An employee inspects molten steel at a plant which recycles scrap metal into steel rods in Kawaguchi, Japan, 2019. Image: Tomohiro Ohsumi via Getty Images.
Different routes to net zero steel
To achieve net zero steel, we will have to use steel efficiently, and maximize the recovery and recycling of scrap. But that is not enough. We also need to produce net zero steel from iron ore – and at scale.
In 2050, there are likely to be fewer sites making steel from iron ore than there are today. Those that do will do it through a combination of technologies: using green hydrogen as fuel, through direct electrolysis of iron ore, through carbon capture and storage and through the use of biofuels. Furthermore, all steelmaking sites will be using power generated from renewable or other zero-carbon resources. Figure 2 illustrates the change that needs to take place.
Figure 2: Illustrative greenhouse gas emissions intensity distribution of steel making sites in 2020 vs net zero emission sites in 2050
Source: Author's own illustration
The problem with ‘low carbon’ steel
What can policymakers, steel users and specifiers do to support the transition? The obvious response is to set specifications to use steel with lower embodied carbon. It seems like a no-brainer: if steel buyers and specifiers create more demand for low-carbon steel then market forces will work their magic and policy measures can also be put in place to favour low-carbon steel.
As we have seen, the easiest way for steel-makers to reduce the greenhouse gas emissions intensity of their steel is to use more scrap whether by increasing the proportion used in a blast furnace or using 100 per cent scrap in an electric arc furnace shown by Approach 2 in Figure 3. Importantly, the world’s most inefficient steel-maker can produce steel from scrap, even using coal-generated electricity, with a lower carbon intensity than the world’s most efficient steel-maker making steel from iron ore.
The problem is that if the supply of scrap is limited, and the global demand for steel is not reduced significantly at the same time, then the outcome is that scrap will be diverted from one steel-maker to another without reducing the greenhouse gas emissions for steel-making overall.
At the same time, there is little incentive for steel-makers – whichever method they use – to take the harder decisions and make the long-term investments to reduce their greenhouse gas emissions for a given level of scrap input. Site-level emissions can be lowered through efficiencies, new technology and more use of renewable energy shown as Approach 1 in Figure 3.
Figure 3: Approaches to reducing emissions from steel production
What this means is, specifying the carbon intensity of steel on its own is an inefficient means to support emissions reductions in the steel sector. A mechanism is needed that rewards producers who reduce emissions for all production routes and is not short-circuited by simply shifting the allocation of scrap.
A better way to specify
That mechanism is not hard to devise. It is to define performance levels on the basis of the greenhouse gas emissions intensity for the production of crude steel at a site taking account of the proportion of scrap used.
This measure is applicable to all steel-making sites irrespective of their production method. It differentiates between the better and worse performing electric arc furnace producers as well as between the better and worse performing blast furnace-basic oxygen furnace producers. It also accommodates any other existing or new technologies too.
It also neither favours nor disfavours regions of the world depending on their access to iron and steel scrap so it doesn’t penalize regions with a lower existing stock of steel.
The measure applies to the production of crude steel at the level of a steel-making site so there is no need to carry out a new calculation for every steel product or product category. Every product from a given site can be covered by the same performance measure, referencing the greenhouse gas emissions intensity for the production of the steel the product is made from.
A single performance threshold can be set or multiple levels can be used to differentiate performance along the lines of the European Union’s well-established energy efficiency labels as illustrated hypothetically in Figures 4 and 5.
Figure 4: Building off the EU's energy efficiency label to measure steel-making performance
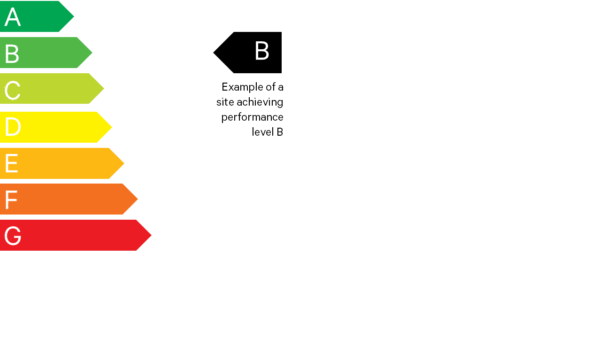
Source: Author's own illustration; European Commission (2021)
Thresholds can be aligned with other definitions, for example, ‘lower embodied carbon’, ‘near zero’ or ‘net zero’ steel. Performance bands can then be used for multiple purposes: as marketing and communications tools by steel-makers, as steel purchasing specifications for public or private procurement or as a basis for policy measures such as carbon border adjustments.
The intent would be to support those steel-makers currently considering whether – and just as importantly, when – they will make investments in new technologies.
Steel-makers need to be recognized for setting forward-looking decarbonization targets but they also need to know that the market will rewarded their investments in reducing greenhouse gas emissions from steel made from iron ore and, additionally, that sites producing this steel will not be undercut by those simply using more scrap as an input.
Figure 5: An illustration of performance banding for crude steel greenhouse gas emissions intensity
Source: Author's own illustration; Underlying data from the CRU Steel Cost Model and Emissions Analysis Tool (2021)
The specification of crude steel site performance in this way does not make a product-specific carbon footprint redundant but gives it added value.
For a given performance level, the product with the lower absolute greenhouse gas emissions intensity should still be preferred. Steel users can still use data about absolute emissions of products to monitor their embodied carbon emissions over time and to make comparisons with products made with other materials. They can and should continue to use less steel to do more, avoid waste and work to make steel products more reusable and recyclable.
Crucially, more greenhouse gas efficient steel-making is not an alternative to material efficiency or vice versa – the world needs both. By comparing the greenhouse gas emissions of steel-making on a standardized basis, taking account of the proportion of scrap used, customers, policymakers and other stakeholders can incentivize more carbon-efficient steelmaking and avoid the risk that their actions simply drive the re-allocation of scrap from one customer to another.
Matthew Wenban-Smith is the GHG Lead for ResponsibleSteel. ResponsibleSteel is a multi-stakeholder organisation developing an international standard for responsible steelmaking.