Circular Economy & Decarbonisation: Lessons from Industry
High quality recycling of industrial materials is a key strategy for delivering a low carbon circular future, argues John Gardner.
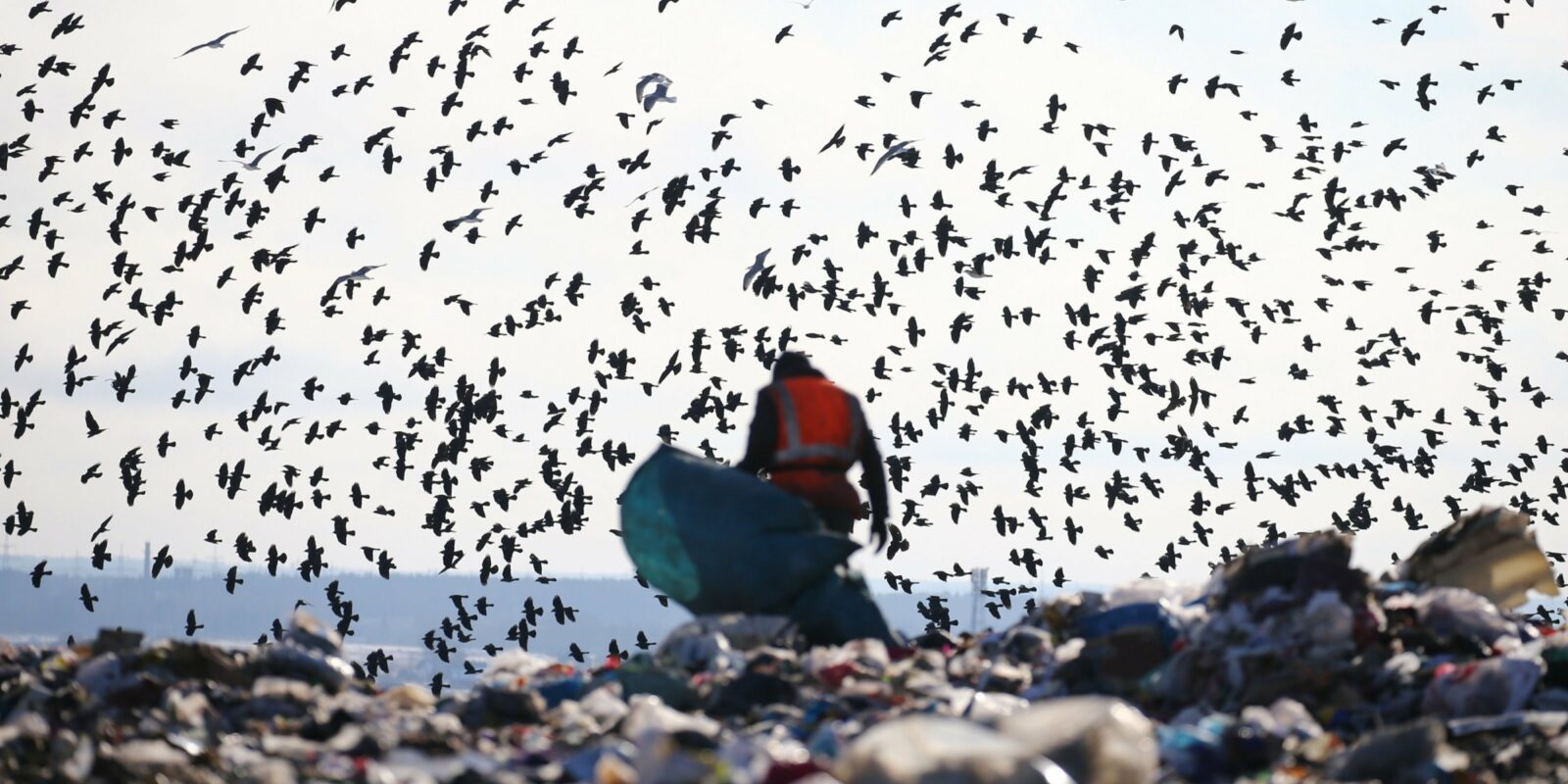
Solid waste landfill in Leningrad Region, Russia. Image: Peter Kovalev/TASS via Getty Images.
Following decades of concerns over resource security, the concept of a circular economy is fast becoming appreciated as a more inspiring solution. At its core, it involves including materials within a growing economy for as long and as efficiently as possible.1 Optimizing material flows and use within a circular economy context often involves designing:
-
Products with materials and designs that best enable reusing, refurbishment, remanufacturing and recycling;
-
Sharing mechanisms that can also extend the life of products;
-
Waste management systems that retain the quality and value of materials, including through recycling.
Proponents argue that a circular economy can deliver productivity gains2, reduce the environmental impacts of material production and disposal3 and create jobs4 in support of the delivery of all the Sustainable Development Goals5. They also increasingly point to the range of opportunities for dramatic greenhouse gas (GHG) emissions reductions through avoided primary material production, such as bauxite for aluminium, or landfill-related emissions.6
Despite these potential benefits, what remains unclear is how best to transition from the more established ‘linear’ system of material extraction, use and disposal. Some circular strategies require a significant departure from business-as-usual activities, but others only require mere improvements on long-established practices and are therefore simpler to implement. Recycling, also referred to as secondary materials production, fortunately falls in the latter category.
Recycling to increase circularity
In many countries recycling value chains are already well developed, with increasingly efficient systems for collection, separation and processing of wastes or materials that cannot be reused or refurbished. Developments in recent years, including landfill taxes and periods of high oil prices, have also made recycling a relatively more attractive waste management option. However, today average recycling rates in the European Union stand at around 40 per cent for household waste and 60 per cent for packaging waste, indicating much room for improvement.7
One limitation of these recycling rates is that they reveal little about the quality or value of the recycled materials. This information is critical for assessing the scope for displacing primary materials production which tends to be more emissions-intensive than recycling.
With the current recycling rates and little clarity around the quality of recycled material, embedding recycling within a broader circular economy framework offers a timely opportunity to align a circular economy with climate change goals.
Maximizing material quality and emissions reductions
Recycling can be either open- or closed-loop. Which option is deliverable is a function of the quality of the collected waste or material, supply chain capabilities as well as market conditions.
Open-loop recycling means that scrap is recycled and the secondary material is used in a different product to the original. The scrap is often mixed with different grades or alloys so is less pure and is used to make products that can accommodate wider chemistry ranges. Some argue that open-loop recycling forces materials into a down-cycling loop. Others emphasize its important role to enable an exchange of materials between industries.
Closed-loop recycling utilizes waste from a single product or material stream to produce secondary material that can be used in the same product. For example, an aluminium can that is used, discarded and recycled into a new aluminium can. Closed-loop recycling can be used for any material (e.g. paper, glass, plastics and metals) as long as sufficient feedstock is available. For some materials closed-loop recycling can be done indefinitely without the material quality degrading and is therefore often regarded as highly efficient, both environmentally and economically.
An important precursor to open- and closed-loop recycling is consequently an efficient system of waste collection and sorting. Figure 1 shows that the potential energy and GHG emissions reductions from high quality recycling of key industrial materials are sizeable. Research conducted on behalf of the European Commission shows that for aluminum, energy and emissions savings can be up to 90-95 per cent relative to primary production8. For steel it’s up to 85-90 per cent9 whereas for PVC, a commonly used plastic, recycling reduces energy requirements and GHG emissions by two thirds10. A similar study for the US Environmental Protection Agency indicates that recycling glass and paper could reduce energy requirements and emissions by one third compared to primary production11.
That said, there are many reasons why these emissions and energy savings may fall short in reality. Some waste, for example, would need further processing before recycling. An aluminum can is usually covered in a coating that would need to be removed as part of the recycling process (closed-loop can recycling will use coating as fuel to melt the metal). At the same time, waste streams will sometimes be a mix of different materials or material grades which means that the recycled material is lower quality than anticipated. The emissions and energy savings will also depend on the efficiency of the recycling facilities and the fuel mix powering it.
Recycling efforts can have a significant impact in aggregate. For example, in the US, recycling packaging containers avoided around 8.4 million tonnes of CO2 in 2010. While this is impressive, in the same year nearly 10 million tonnes of packaging containers, comprising glass, carton, plastic and metal, was sent to landfill sites – a missed opportunity to save another 12 million tonnes of GHGs12.
Figure 1: Potential energy and GHG emissions savings achieved through recycling compared to primary material production
Sources: European Commission (2012, 2015, 2017), US Environmental Protection Agency (2016). See footnotes 8-11.
Learning from best practice
Action is needed from both the private and public sectors to share responsibility and realize the full scale of the environmental and economic opportunity offered by recycling. Best practice examples are a useful starting point for developing broader lessons around high quality recycling that draws on circular principles.
Case studies of best practice
These examples demonstrate that high quality recycling can present opportunities for new partnerships (Interface) and forms of value creation (Dell), that enable market differentiation (Fairphone) and that can also create a secure supply of secondary materials for use within current manufacturing facilities (Jaguar Land Rover) or in the future (Maersk).
Moving from best to common practice
Further exploration of these and other case studies is needed to reveal how certain companies came to be vanguards of circular thinking in recycling and, importantly, what difficulties they faced along the way. However, even without this in-depth analysis, four broad lessons are apparent.
-
Long-term recycling goals will guide current and future efforts. A recycling target sets the direction of travel and signals a company’s long term commitment. It can also be used to develop a pathway of recycling activities, to benchmark progress and can stimulate demand for investment in recycling infrastructure and equipment and can also influence raw material input sourcing strategy.
-
High quality recycling is enabled by collaboration across the entire supply chain. From designers, material suppliers, brand holders, retailers and consumers to waste managers and recyclers, all stakeholders need to be involved in partnerships to identify who can be engaged in waste material collection, sorting and processing.
-
Product design will be a critical factor in determining the recyclability and value of secondary materials. Making products that efficiently do the job required but can be easily reused or recycled at the end of their life is essential. Products must be made in such a way that materials can be separated into recycling streams and used again in new products. Unnecessary product or material complexity can add significant barriers to recycling, often reducing the relative energy and emission benefits compared to primary production.
- New business models can be applied across the supply chain to drive recyclability and circularity. Whether this is through servitization, product take-back or sharing models, manufacturers can begin thinking about the end-of-life stage of their products and possibilities for value creation through closed- or open-loop recycling.
For these best practice examples to come into the mainstream, it will also require technology development and diffusion. While there has been progress in sorting and separation technologies - such as optical material detection systems and in the energy efficiency and contaminant control of reprocessing technologies - further progress is needed in order to maximize the potential emissions and energy savings from recycling.
The supply of scrap material available for recycling could be expanded through incentives or information-sharing, for example through the use of labels or material passports. Sharing data around the embedded emissions and energy in products could also stimulate demand by making customers aware of the sustainability impacts of their material purchasing decisions.
Finally, the role of governments should not be overlooked. R&D and innovation can be driven by the industry in some part, but policy developments can provide powerful market and price signals, and shape the economics of recycling.
With population growth and an expanding middle class, global consumption levels are rapidly increasing and this will exacerbate the climate change challenge. Moving away from a throwaway society and a linear economy to a more circular one is a key strategy for delivering a low carbon future.
The circular economy is about more than recycling but it’s a good place to start and, as shown through the best practice case studies, there is much room for improvement.
John Gardner would like to thank Simone Cooper-Searle, Anne-Marie Benoy, Bernice Lee and Felix Preston for their contributions to this article.