Making Climate Friendly Cars: Material Considerations
Reuse and recycling can significantly reduce the greenhouse gas emissions impact of the materials used in cars, writes Simone Cooper-Searle.
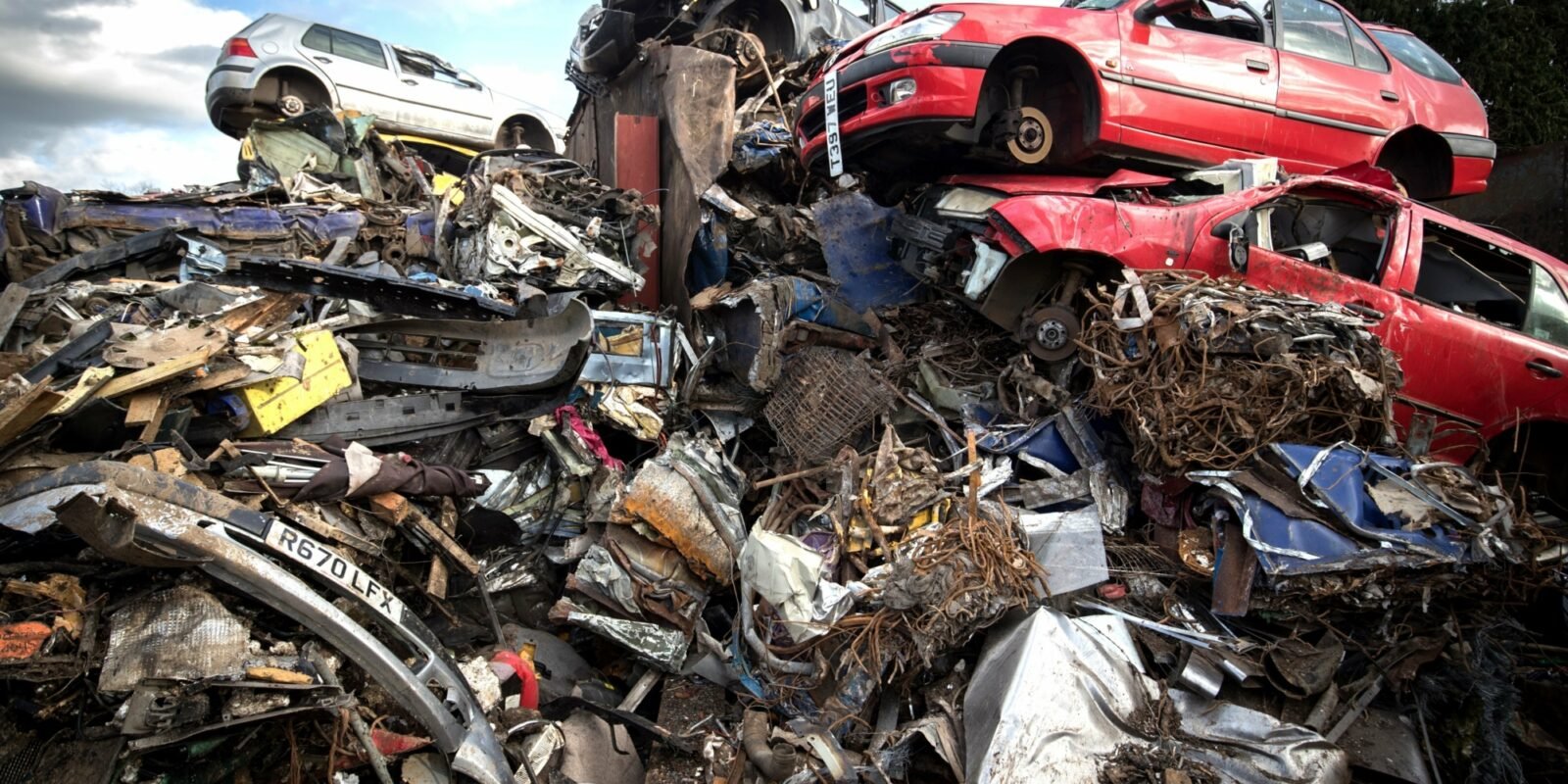
Scrap metal and scrap cars wait to be processed at Pylle Motor Spares and Metal Processing in Somerset, UK. Image: Matt Cardy/Getty Images
The demand for personal mobility is growing. In 2016, the global automotive industry manufactured over 70 million new cars and production is anticipated to reach 100 million by the end of the decade.
Global production of new cars 1990-2020
Source: US Department for Transport, Bureau of Transportation Statistics. 2017. Table 1-23: World Motor Vehicle Production, Selected Countries.; OICA (a), 2017. Production Statistics; IHS Markit, 2016. Automotive Industry Outlook: Navigating the Waters in a Post-Recovery Environment. Presentation by Mike Wall, Director.
Cars comprise thousands of individually manufactured components with iron, steel and aluminium being the main materials used. Each year the global automotive industry uses around 150 million tonnes of these materials.1 However, this production releases large amounts of greenhouse gas (GHG) emissions and, as a consequence, car production is a major driver of material demand and industrial GHG emissions.
Average material composition of a new American car in 2015
When a car has been manufactured and sold it becomes part of the global fleet of automobiles, which currently stands at around 1 billion vehicles. At the end of a car’s working life, materials and components can be recovered and when a car no longer functions as a mode of transport, its value becomes determined by its constituent parts.
Reuse and recycling therefore gives a second life to the materials used in car production. On average, both reusing and recycling material requires less energy and releases fewer emissions than producing new material. Current industry efforts are focused on recycling materials at the end of a vehicle’s life. In Europe, for example, over 90 per cent of the mass of materials recovered from end-of-life vehicles is recycled.2 However, this figure reveals nothing about the quality and value of the recycled material or the GHG emissions impact. A number of steps could be taken before a car is scrapped to increase the quality and value of the recycled materials so they can displace new material and reduce the GHG emissions associated with material use in the automotive industry.
What to consider when making a car
Car design
It seems counterintuitive for designers to think about how a car will be dismantled before it has even been made. Cars need to be durable, secure and perform well in a crash situation. This will rightly be at the forefront of a designer’s mind. However, retaining the quality of recovered materials could be a secondary consideration.
Throughout cars, materials are mixed together in components - like batteries and electronics. At the end of a vehicle’s working life it can be challenging to completely separate, and recycle, these materials. Scrap material, such as steel, can contain unwanted elements, such as copper. Current designs of car components, such as the wiring harness, make it prohibitively time-consuming and expensive for vehicle dismantlers to fully extract copper.3 As a result, some copper is mixed and melted with recovered steel, which is known as ‘scrap contamination’. The result is a less pure, lower quality, downcycled steel. As a consequence, it is estimated that only around 10 per cent of the mass of recovered iron and steel is recycled and used again in cars. The remaining 90 per cent will be used in other sectors where the performance requirements are lower.4 In light of this, vehicle and component designers should be mindful of the need to recover, and separate, scrap material quickly and easily at the end of a vehicle’s working life.
Material sourcing
The problem of ‘scrap contamination’ and material downcycling at the end of a car’s working life means that most steel and aluminium purchased by the automotive supply chain is new material. Those involved with material sourcing could consider whether there are opportunities to purchase new materials with relatively lower embodied GHG emissions. This might mean finding materials that are manufactured using renewable energy sources. BMW, for example, uses carbon fibre that is produced using only hydroelectric power.
An alternative approach to material sourcing involves looking closer to home. New material purchased by manufacturers in the automotive supply chain usually comes in standardized shapes and sizes. It is then cut and formed to make individual components, which generates manufacturing scrap. For example, only around half of the sheet metal purchased to make a door actually ends up in a car.5 If there are no options to reduce the amount of scrap generated, it could be recycled back into the automotive supply chain.
In a controlled factory environment, ‘scrap contamination’ may be less of a problem and the quality of the recycled material could be maintained. The REALCAR project - a partnership between Jaguar Land Rover (JLR) and aluminium producer Novelis - is a recent example of high quality scrap recycling in practice.6 In one year, 30,000 tonnes of press shop aluminium scrap were recovered from JLR plants and recycled by Novelis, to be incorporated into new body panels. The REALCAR project involved material innovation to create a new aluminium grade best suited to the controlled recycling process. It also necessitated new forms of supply chain cooperation and changes to production practices. Those involved with sourcing material will therefore need to consider whether securing an internal supply of recycled materials requires broader changes to their business model.
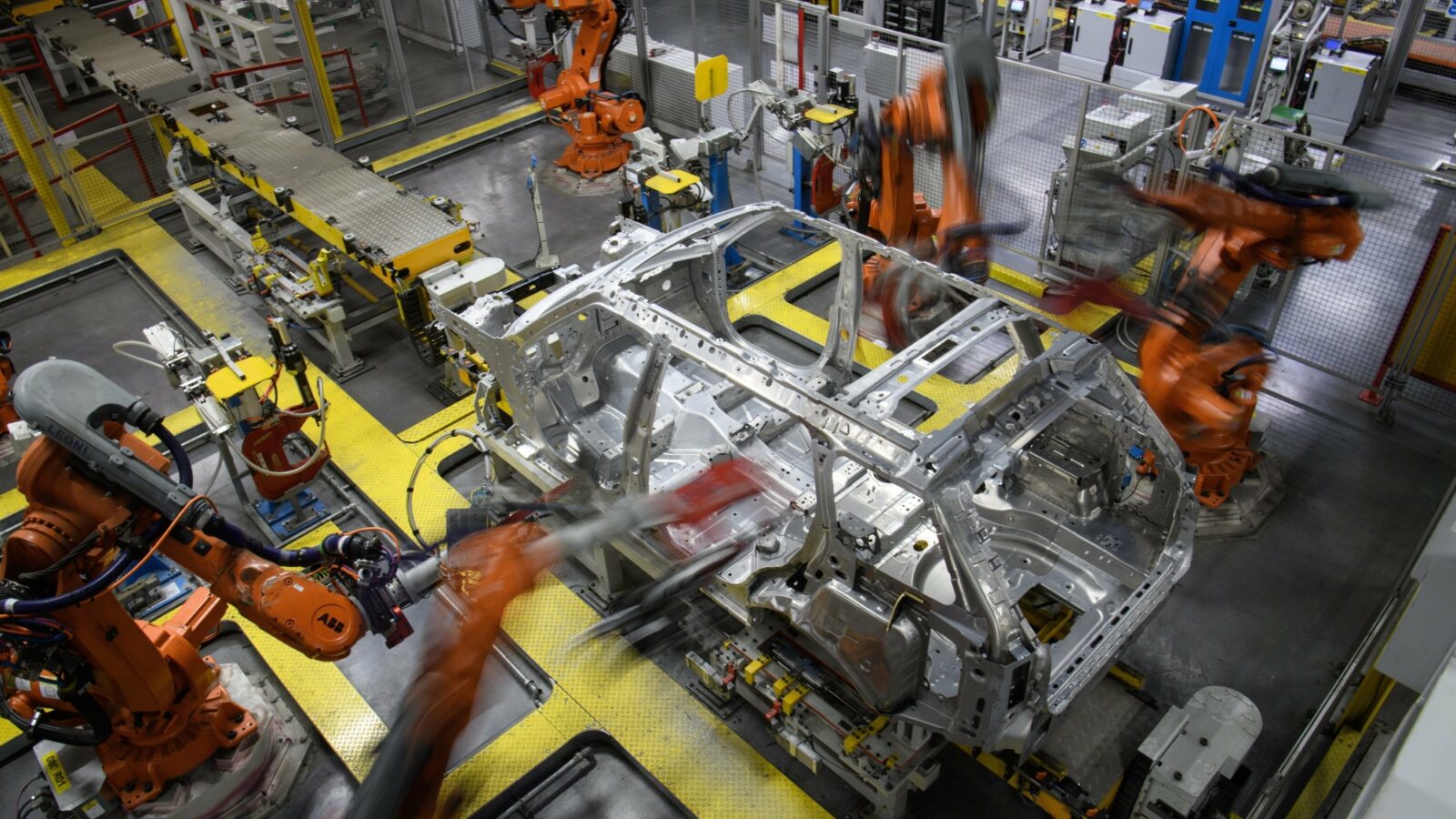
Robotic systems work on the chassis of a car during an automated stage of production at the Jaguar Land Rover factory in Solihull, England. Image: Leon Neal/Getty Images
Manufacturing scrap material
If vehicle and components manufacturers aren’t able to recycle and use manufacturing scrap themselves, they should explore whether other firms can. In the UK, for example, Abbey Steel purchases and processes scrap sheet metal from the production lines at large automotive manufacturers including Honda and JLR. The steel is then sold to manufacturers of small metal components such as filing cabinets and electrical connectors. Around 10,000 tonnes of steel are cut and resold by Abbey Steel every year. Since the steel supplied by Abbey Steel doesn’t need to be re-melted or coated, around 55,000 tonnes of CO2 emissions are avoided.7
Blue Star Steel in the USA similarly buys scrap steel from General Motors and reprocesses it to make components for heating and air conditioning equipment. Manufacturers should therefore be mindful of the needs of customers like Abbey Steel and Blue Star when handling their scrap. There are more options for reusing larger pieces of manufacturing scrap while smaller pieces may only be suitable for recycling.
What to consider when repairing a vehicle
Remanufactured components
Companies involved in repairing cars often need to replace broken components and can choose to use new or second-hand parts. The latter is far superior from a material, and energy, standpoint. The Automotive Parts Remanufacturers Association (APRA) suggests that remanufacturing can produce material savings of up to 85 per cent and energy savings of 45 per cent compared with the use of a new component.8
Importantly, using second-hand components doesn’t mean sacrificing quality. Around fifty different components can be extracted from end-of-life vehicles - disassembled, cleaned, remanufactured and certified that they are as good as new. APRA also suggests that a remanufactured part can be 25-50 per cent cheaper to make than a new component. Some companies have already capitalized on these business opportunities. Caterpillar, for example, a producer of large industrial machinery and equipment, sells remanufactured components alongside its new products.
Interestingly, the global market for remanufactured automotive components is more established than the market for reusing manufacturing scrap. In Europe, for example, sales of remanufactured automotive components generated revenues of approximately €7 billion in 2015. While this is impressive, there are likely to be opportunities for more market growth given that the annual volume of European sales in spare parts is around €100 billion.9 Prioritization of remanufactured - over new - components by companies involved in repairing vehicles could stimulate demand and encourage more companies to engage with remanufacturing.
Supporting further reuse and recycling
The suggestions outlined are yet to become common practice. A range of barriers can explain why reuse and high quality recycling is not taking place on a wider scale. For example, companies that reuse material will be competing for manufacturing scrap with more established companies that downcycle materials. Technological advances also mean that many vehicle components are becoming more complex and diverse. This will make remanufacturing more challenging - and costly - if companies have to spend more time repairing components and hold a larger inventory to guarantee they have the right parts in stock.
These barriers are speculative, however. Further research into the challenges and opportunities of reusing, recycling and remanufacturing car materials is needed. We can only understand why reuse and recycling is not commonplace through discussion with firms along the automotive supply chain and those pioneering companies who are trying to do things differently. This will help identify the operating circumstances under which it’s preferable to reuse and recycle, and pave the way for new efforts and partnerships in this area.
In light of growing demand for personal mobility in an era of climate change, the automotive supply chain should be encouraged to do all it can to reduce the impact of the materials it uses on GHG emissions.