Lower Carbon, Less Materials: A ‘Systems’ Approach
Material efficiency could reduce industrial GHG emissions but has received relatively little attention to date. A 'systems' approach to policy formation is now needed, writes Simone Cooper-Searle.
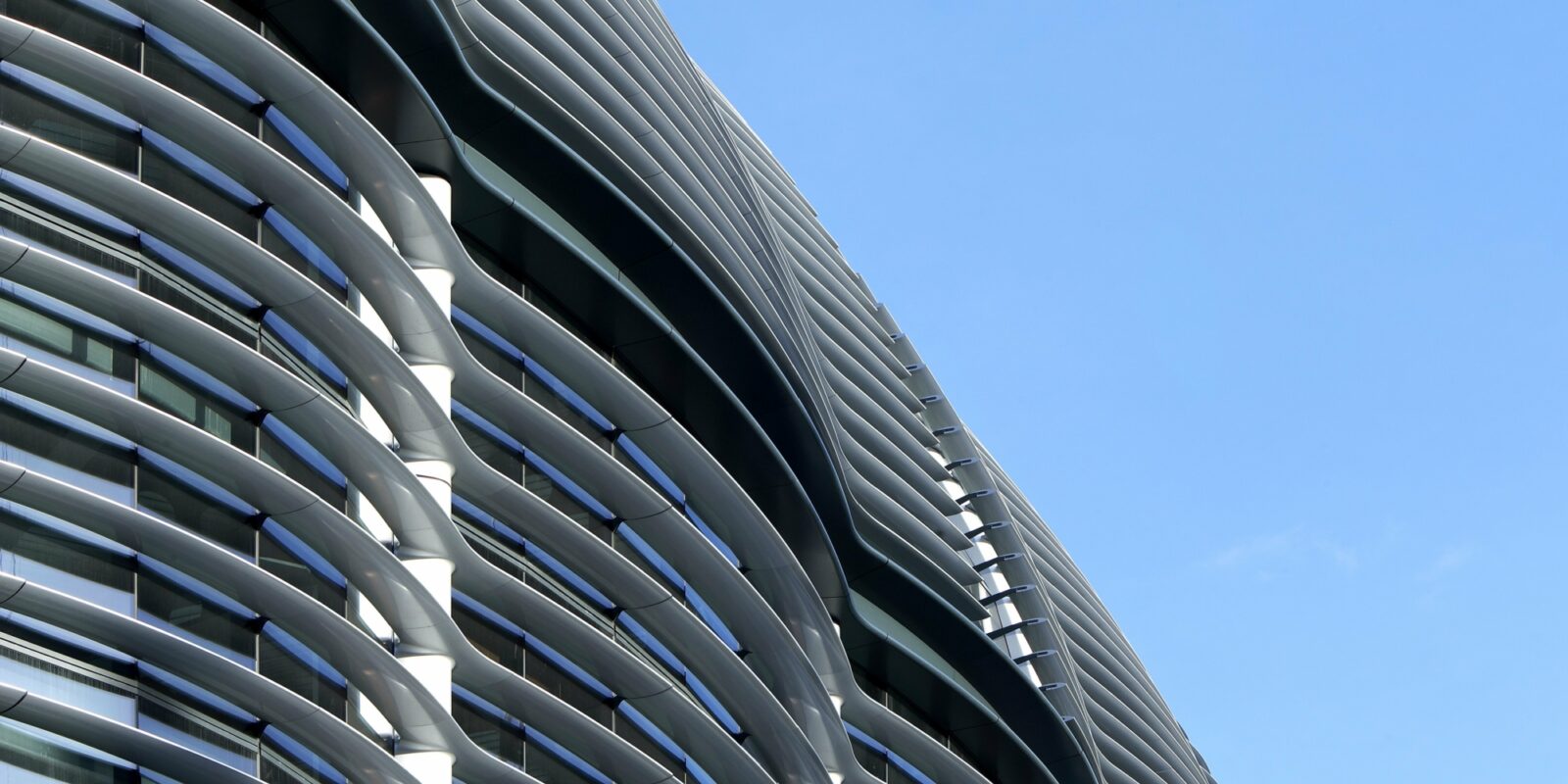
The exterior of The Walbrook in London, UK is made using energy efficient fibre enforced polymer materials. Image: View Pictures/UIG via Getty Images
Introduction
Around the world, national governments have committed to achieving deep, long-term reductions in greenhouse gas (GHG) emissions in response to the global climate challenge. To date, much of these efforts have gone into reducing carbon emissions from the energy sector and avoiding deforestation. Recent years have seen greater attention on another major source of emissions – namely those from industrial processes.
Around a quarter of all GHG emissions are released during the transformation of minerals, fuels and ores into materials such as steel, cement, plastics and aluminium.1 These materials are used to manufacture products central to households and industry, including vehicles, buildings, machinery and appliances.
On the supply side, some efforts are underway to reduce the emission intensity of these production processes. A complementary strategy is to explore opportunities around how these materials are used. More efficient use of materials could reduce material demand and further reduce industrial GHG emissions. Despite its potential, the Intergovernmental Panel on Climate Change recently observed that ‘material efficiency’ has received relatively little attention to date.
The aim of material efficiency is to deliver the same products and services with less new material. A variety of strategies could be introduced throughout the lifespan of a product to achieve this goal. For example, from the outset product designers can select lightweight, high performance materials. They can also reduce the amount of materials needed by reducing product dimensions or designing a product in a way that minimizes its weight. Furthermore, during product manufacturing, companies can focus on reducing the amount of scrap material that is generated. If scrap material and waste cannot be avoided, there may be options to reuse or recycle manufacturing scrap. Reusing and recycling material tends to generate fewer GHG emissions than producing material from new sources.
Once a product has been manufactured and sold, further opportunities for material efficiency depend on how the product is used. If products are repaired and then kept for longer, demand for new products can fall. Similarly, if products are shared between individuals then overall demand for products could also fall. Finally, at the end of a product’s working life, there may be opportunities to repair the product, which would allow all, or parts, of it to be reused. Alternatively, a product could be dismantled and its constituent materials could be reused or recycled.
Options for improving material efficiency
Selecting the most appropriate material efficiency strategy - or strategies - to reduce GHG emissions can be challenging. The emissions impact of each option will depend on how materials and products are manufactured, used and disposed of at the end of their working life. There are also potential trade-offs: for example, if a product is shared and used more intensively, it may become worn out more quickly and need to be replaced more often, which can generate demand for new material.
The variety of options for improving material efficiency, and the complexity of choosing between them, can make them unappealing to firms that are looking to reduce their GHG emissions.
The International Energy Agency has identified two further barriers. First, industries lack expertise on how to improve material efficiency. Second, cost structures and tax regimes often mean labour is more expensive than materials: firms are less likely to introduce material efficiency improvements if their employees take longer to manufacture a product.The reality is, without appropriate policy incentives, firms may continue to prioritize other GHG emission reduction strategies and overlook opportunities for material efficiency improvements. However, there remains scant policy interest in material efficiency as a GHG emissions reduction strategy: among EU countries, for example, improvements in material efficiency are mainly viewed as waste management and recycling strategies.2 So why is this the case and what can be done about it?
Why is there a lack of policy interest?
Country targets are focused on domestic GHG emissions
Many countries around the world have set targets to reduce their GHG emissions. Most of these country-level targets are focused on domestic emissions i.e. those generated within a country. For example, China, the world’s largest country-level emitter, intends to reduce the GHG emissions intensity of its economy by 60-65 per cent below 2005 levels by 2030.3 However, a focus on domestic emissions will ignore much of the potential reduction in emissions that material efficiency could deliver if those reductions happen abroad. Cars, for example, are traded internationally. If a country such as Australia - a large net importer of new cars - introduces policies that encourage its citizens to share cars or keep them for longer, there will be a reduction in car demand. Assuming this leads to a fall in car production, fewer GHG emissions will be generated. However, this won’t be recognized as a contribution to Australia’s climate change target.
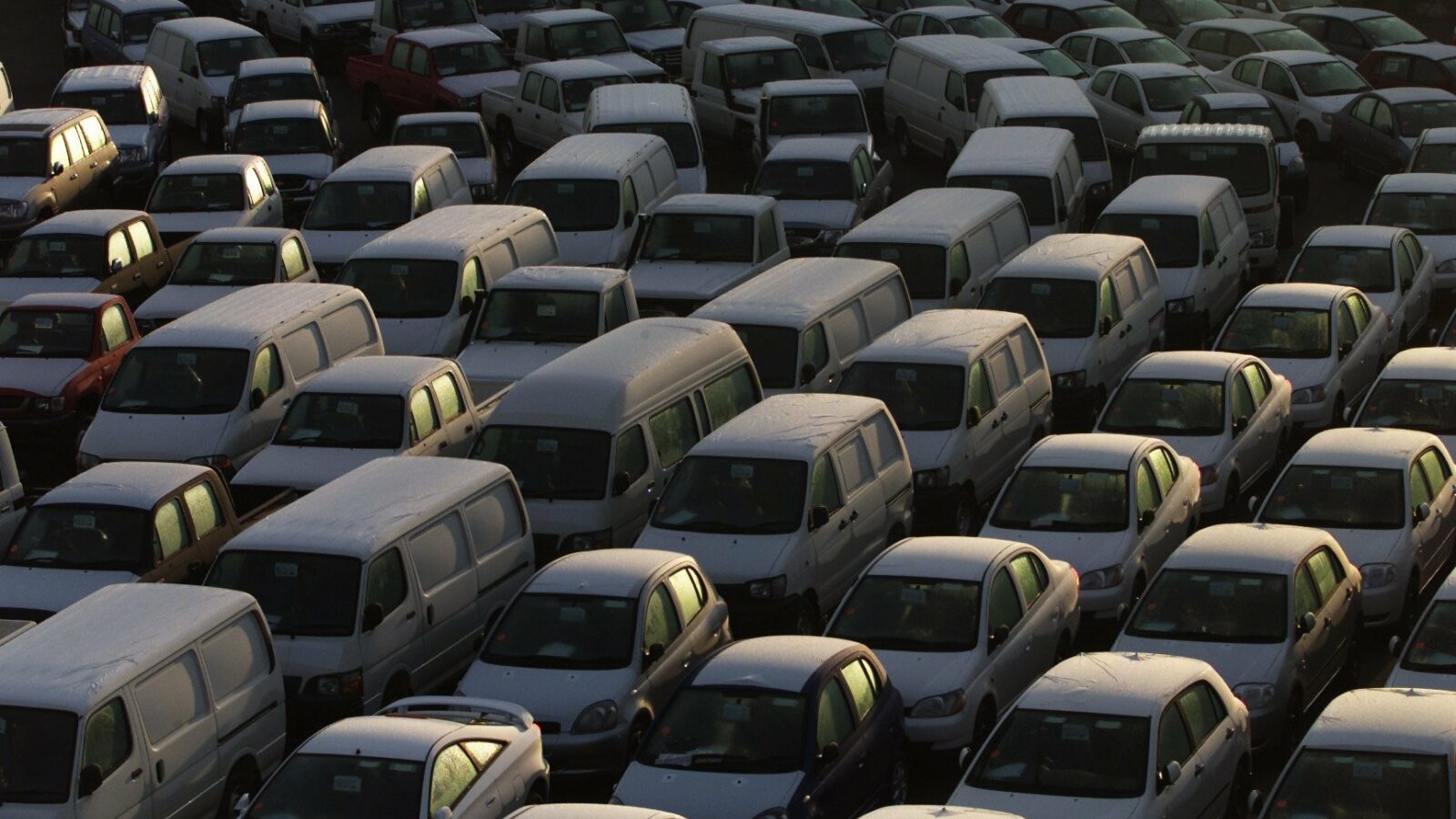
Imported vehicles parked at the docks in Sydney, Australia. Image: Fairfax Media via Getty Images
Sectoral approaches to climate change policy
Most countries that participate in the regular UN climate change negotiations have developed sector-level action plans to help them meet their national targets. Germany, for example, has set goals for emissions reductions by 2030 in the buildings, transport and industry sectors.4 This sectoral approach encourages policymakers to focus on how materials and products are manufactured in each sector and whether this can be done in a way that generates fewer GHG emissions, for example, by introducing new technology or equipment. Identifying opportunities for material efficiency improvements requires a broader perspective that also considers how materials and products are used between sectors. There may be opportunities for ‘industrial symbiosis’ if, for example, scrap material from the production line in one sector can be used, instead of new material, as an input for another sector. There is therefore a risk that when policymakers focus their attention on individual sectors, opportunities to reduce GHG emissions across supply chains and product lifecycles are overlooked.
A lack of a common understanding of material efficiency opportunities
The European Environment Agency recently suggested that there is currently no uniform definition or even implicit understanding of ‘materials’ in EU policy documents and that most member states’ policies leave this term undefined. Without a common definition of materials, how can policymakers be expected to have a common understanding of material efficiency opportunities? There is therefore a risk that policymakers only view some, rather than all, of the strategies outlined as potential opportunities to reduce GHG emissions.
Technical challenges with tracing materials and GHG emissions
A key challenge for policymakers is that there is little data on GHG emissions associated with material use. Although a number of countries report the total mass of material that is used each year, there is little detail on which sectors are using what materials, where in the world these materials come from and what GHG emissions were generated during their production.
Moving from material to product supply chains involves even more complex calculations. A car, for example, comprises thousands of individually manufactured components that are made up of multiple materials, often produced in a global supply chain. Estimating these supply chain GHG emissions would be time-consuming and may require guesswork if there is no information about how and where components are made. This missing data is important. If policymakers do not know what GHG emissions are generated along a product supply chain, how can they assess the emission reductions from improvements in material efficiency?
Poor coordination among material efficiency advocates
The material efficiency strategies explained are not new. Many organizations have spent years promoting them as solutions for a circular economy. However these strategies are not always framed as a way to reduce GHG emissions and this affects how they’re perceived by policymakers. The European Commission, for example, viewed lower emissions as a ‘wider potential benefit’ of a circular economy rather than a primary driver.5 This demonstrates a broader challenge within sustainability: action to address one issue may impact other areas and these interactions between sustainability goals may not be fully understood or communicated.
Towards a ‘systems’ approach
A new, more systematic approach is needed to identify opportunities to reduce emissions through material efficiency. This would help governments evaluate whether material efficiency strategies should be part of the policy mix.
A systematic approach to identifying emissions reduction opportunities
This systematic approach offers a new way of framing opportunities for reducing GHG emissions through material efficiency improvements. Given that a sectoral approach won’t reveal the complete set of options available to reduce emissions, individual sectors need to be viewed as part of a larger economic system. Such an approach demonstrates that consideration should be given, for example, to:
-
User opportunities Encouraging individuals to repair and maintain products and keep them for longer.
-
Producer-user opportunities Providing customers access to a shared product or service.
-
Inter-supply chain opportunities Manufacturing scrap material from one firm being used as an input by a firm making a different product.
-
Intra-supply chain opportunities Reusing or recycling manufacturing scrap within the same supply chain.
-
Product lifecycle opportunities Recovering material and products at the end of their working life and reusing or recycling them as an input into the same supply chain.
-
Economy-wide opportunities Designing products across multiple supply chains for disassembly and extracting the material to displace new material sources.
-
International initiatives Any of the above initiatives adopted by multiple countries.
Material efficiency in practice
Shifting to a ‘systems approach’ requires a change in mindset, not least because it requires collaboration between sectors. This means a new role for governments and advocates of material efficiency to form networks and share information on opportunities between those who are generating material waste and those who could use it. Collating good practice case studies to demonstrate the potential for material efficiency and launching supply chain initiatives which encourage firms to design products that can be easily dismantled and repaired, can also stimulate the reuse or recycling of material.
Implementation also requires a change in how emission reductions are accounted for. Material efficiency opportunities may transcend national boundaries, as product supply chains are often international. Around a quarter of global GHG emissions are generated during the manufacturing of products that are then sold abroad. There needs to be a formal way of recognizing that action taken in one country (e.g. extending the life of a product) could lead to emissions reductions abroad (e.g. reducing demand for new material). Otherwise these emissions reduction opportunities may fall through the cracks. The current focus on domestic emissions targets offers little incentive to reduce the GHG emissions that are embodied in internationally-traded products and services.
Last but not least, a ‘systems’ perspective is also needed to evaluate the impacts of material efficiency. While material efficiency can help reduce emissions, a reduction in demand for new materials can have wider sustainability impacts: for example, there could be a reduction in upstream environmental impacts associated with mining or in the demand for energy if a material is reused or recycled instead of being produced from new sources. Downstream, there might be a reduction in waste material that needs to be processed. Further work is needed to map out the full potential sustainability impacts of material efficiency and other emission reduction strategies.
Looking forward, there are opportunities for a transition towards a systems approach to policy formation. For example, Germany has proposed a new ‘G20 Resource Partnership’. This could act as an important step towards ambitious, coordinated policy action on material efficiency and better data collection and management to track flows along global supply chains.